Since the 16th century Britain had been producing and exporting buttons. However, as the cheaper plastic button grew in popularity, the industry took a major blow. By 2012, after 155 years of business and having once been the largest horn button maker in the world, the last remaining traditional British button factory was closing its doors. In steps Country Life Magazine with a final appeal not to lose this historic British industry…
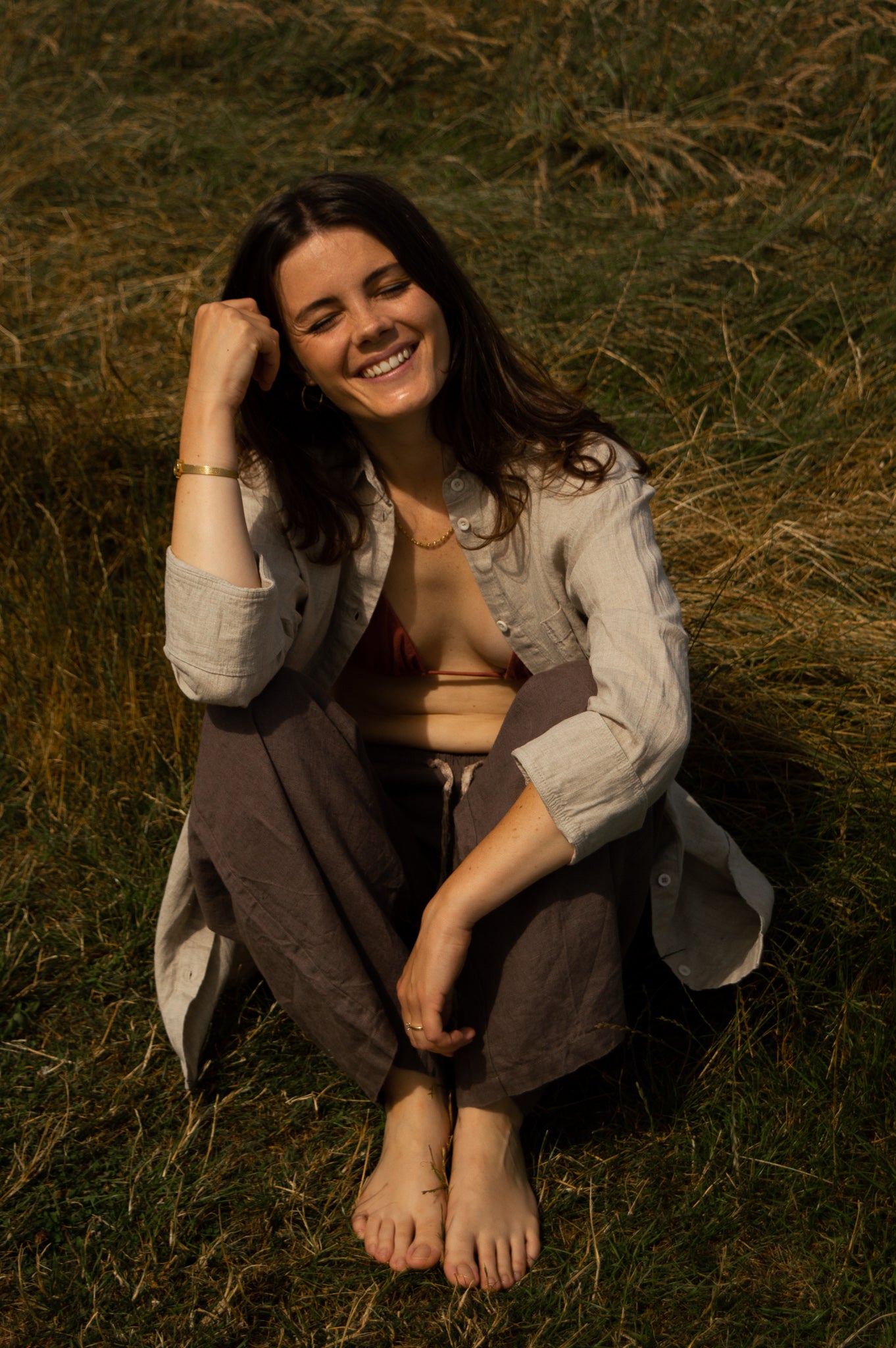
In June 2013, having responded to the appeal, husband and wife team David and Andrea Courtney secured the last button-making and finishing machines, along with historic button dies, sample books and memorabilia.
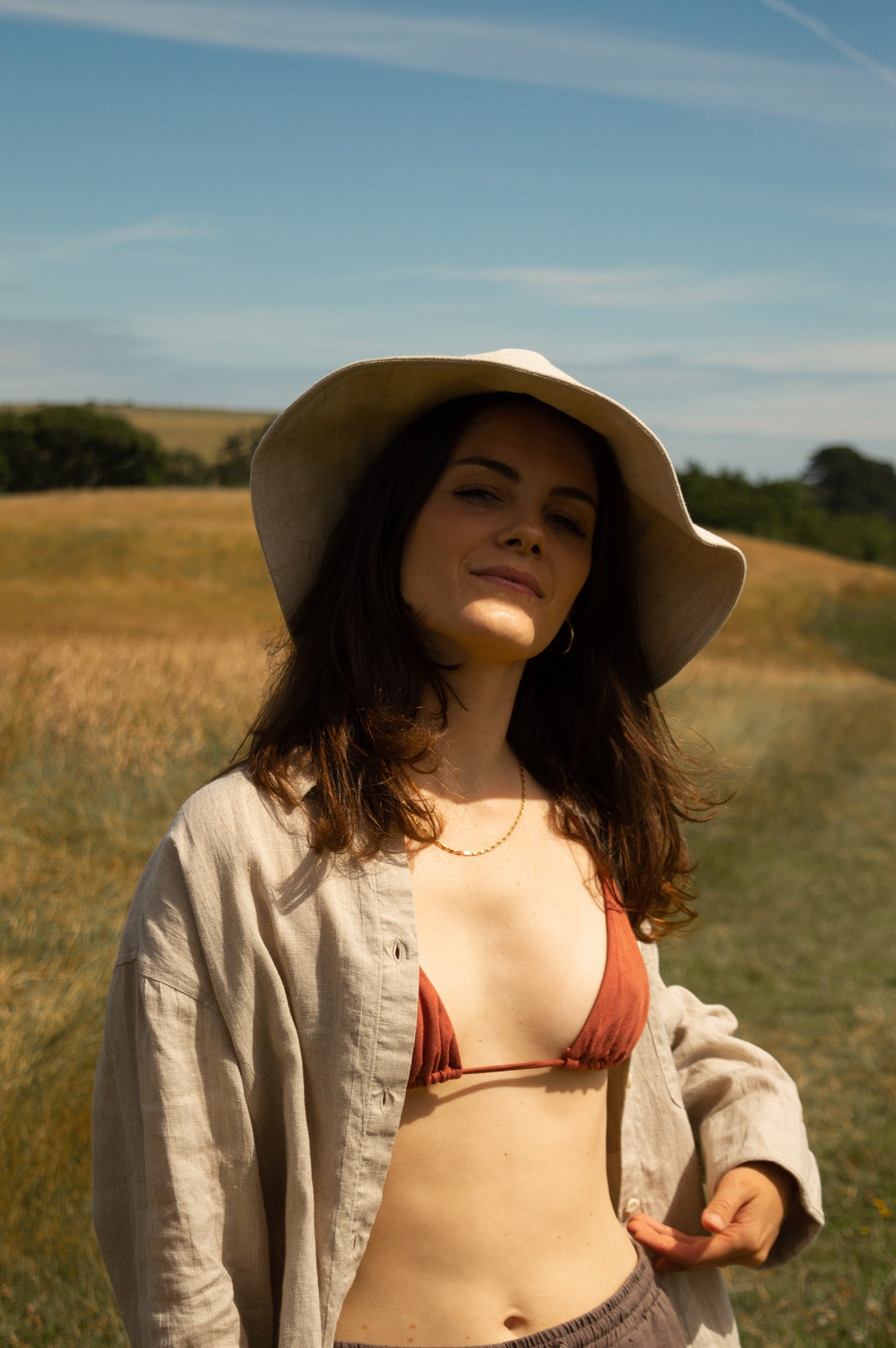
With the belief “nature and fashion can not only co-exist but nourish one another symbiotically” and “there is no better supplier of the most diverse and beautiful materials than nature itself”, Courtney and Co use the finest natural materials throughout the manufacturing process. Whether it’s the nut of the Tagua palm being used to create Corozo buttons, British milk being used to create Codelite® buttons, or even pumice (volcanic ash) and wooden pegs in traditional barrels being used in the final polishing processes, every step of production supports the company’s ethos of “provenance, bio-degradability, sustainability and environmental impact”.
Corozo
“Every time you wear a garment with tagua buttons you are saving a tree, you are doing your part for conservation, defending the world and combating climate change”
Francisco Luna, Tagua Expert
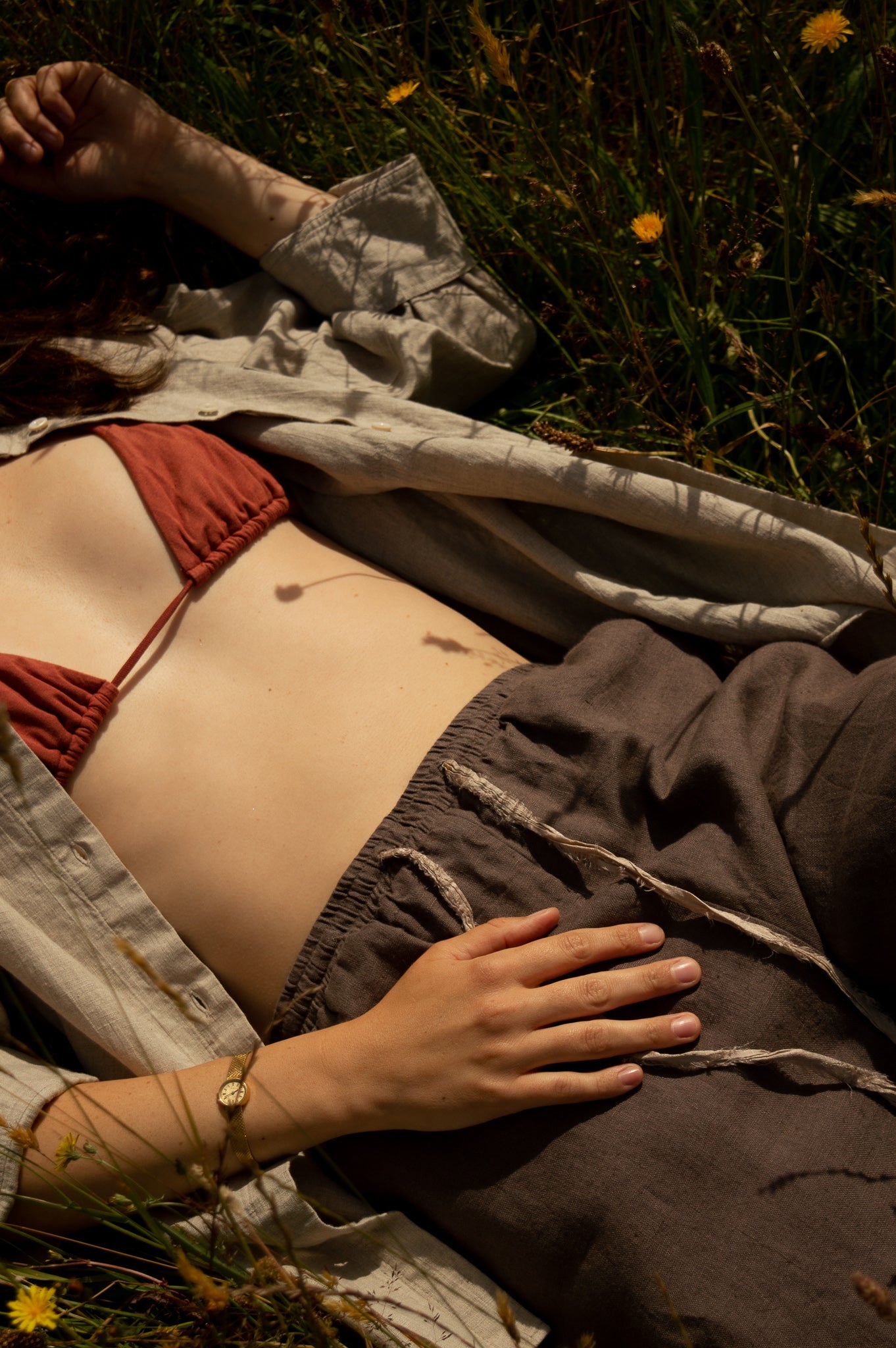
Derived from the nut of the tagua palm, the Corozo material is harvested from the wild rainforests of Ecuador. The tagua palm may take 15 years to produce its first crop, but these nuts will then be harvested from this same tree for a century or more. This is cruicial, as these trees are unable to be planted and thus must be looked after to preserve the rainforest and its many ecosystems. Protecting these trees allows the local people in the rainforest to make a living without turning to deforestation.
-
From each mature tree 15 spiny balls named ‘mococha’ will naturally fall to the ground. Each of these coconut-esque balls contains around 20 little pockets filled with six nuts. This means a single tagua palm tree can produce 1,800 nuts per year - enough for thousands of Corozo buttons each and every year! The animals of the forest feast on the shell of the seed and the local people then retrieve the nuts and generate a sustainable income for their families.
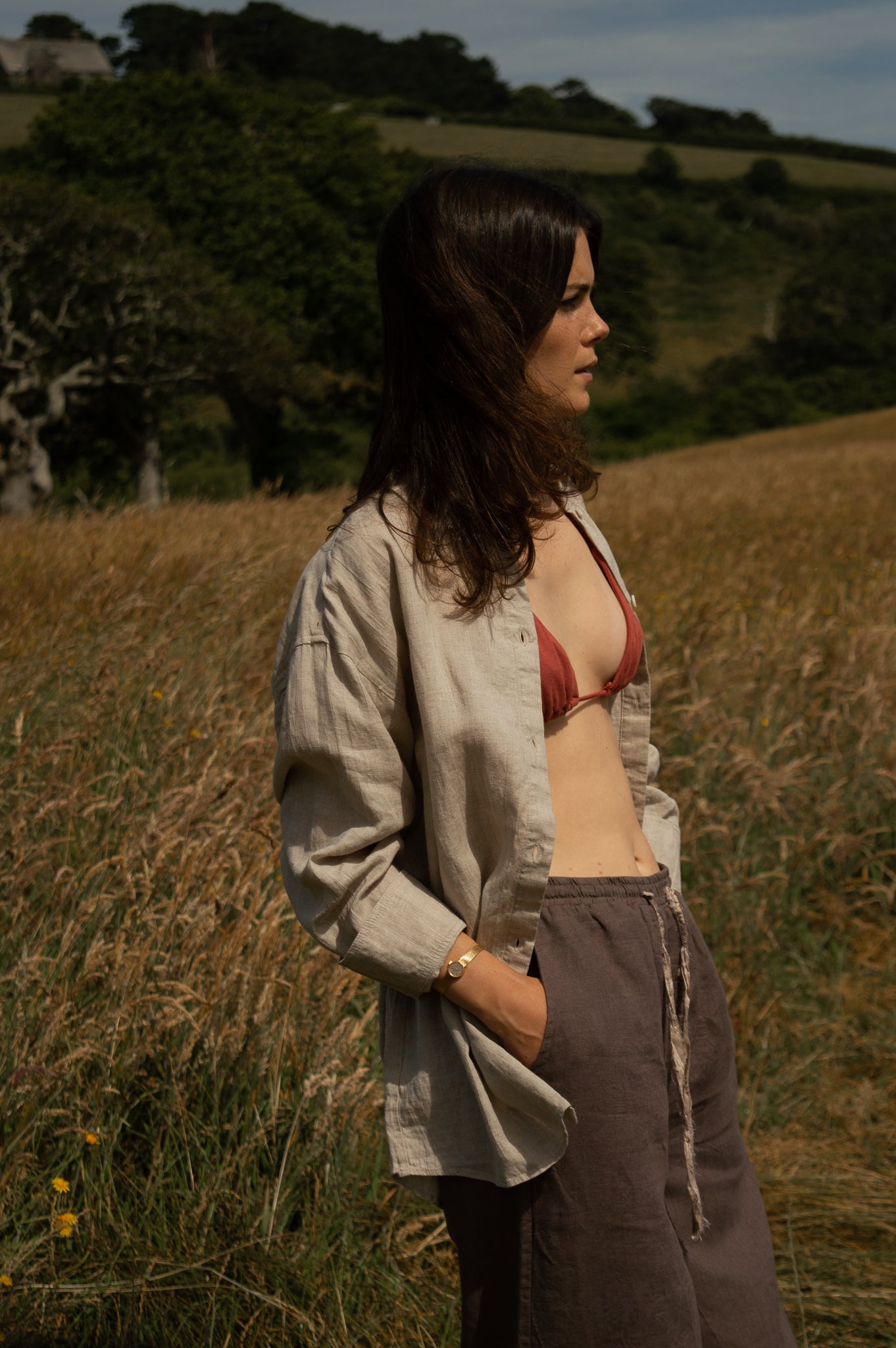
As the harvesting occurs once the nuts have naturally fallen, this means the tree can live untouched and undamaged throughout its life. This great sustainable and economic value provided by the tagua palm also means these rainforests are protected by the people. Tagua art and handcrafts are also able to replace those of ivory, and tagua powder is used in cosmetics as an environmentally friendly replacement to plastic microbeads.
Who knew such good could be achieved through one tiny button!
Codelite®
Though it might seem hard to believe, the UK has been making buttons from milk since 1910
Yes - milk!
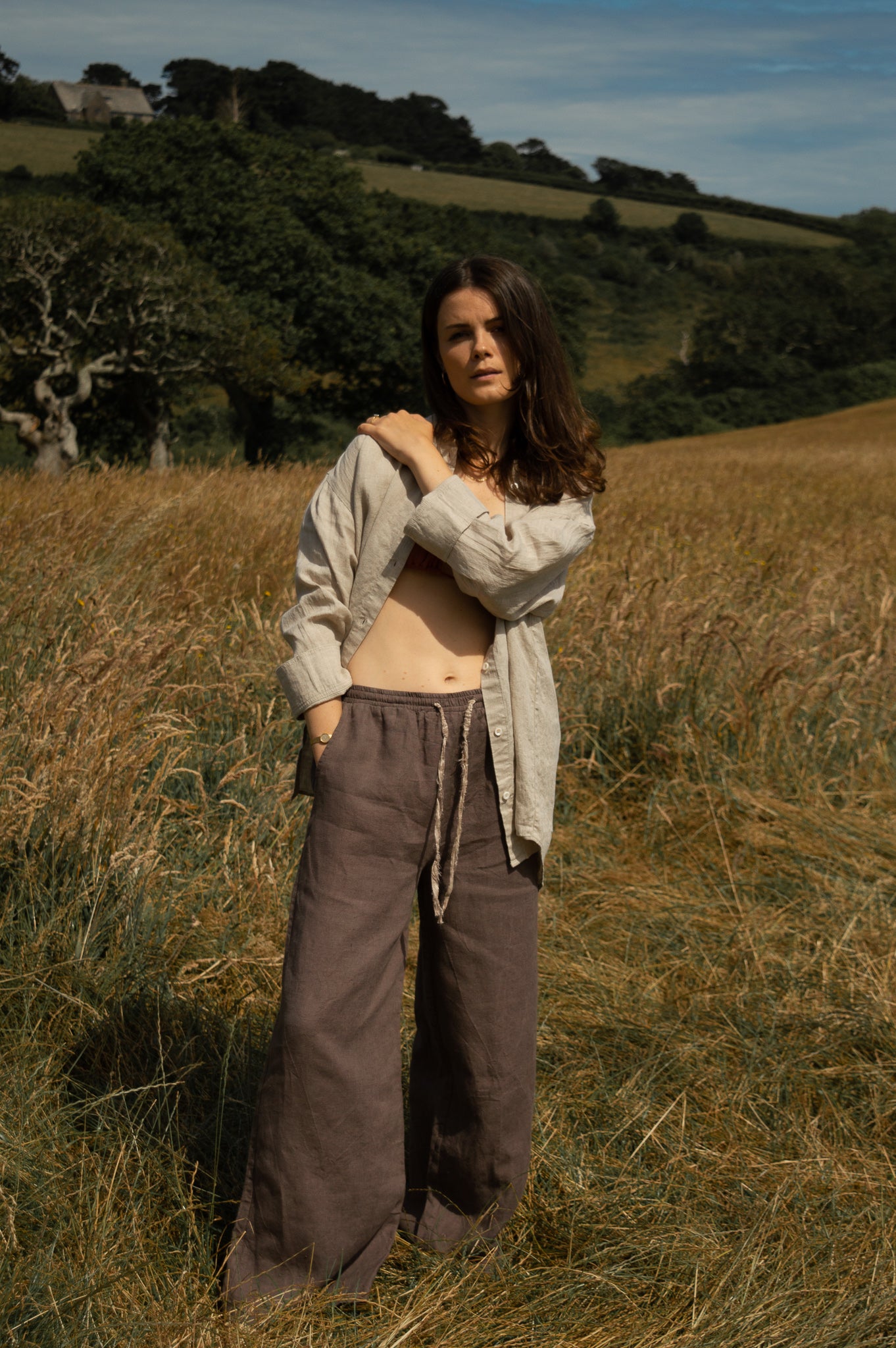
In 2018, after an almost half century gap in production in the UK, Courtney and Co launched buttons made of Codelite® (otherwise known as milk casein).
Casein, the protein element naturally occurring in milk, once cured and hardened in sheets or rods, quickly became a staple for button making. However, with the growing popularity of polyester buttons in the 60s and 70s, milk based buttons became obsolete. Courtney and Co’s modern, state-of-the-art, version of milk casein is known as Codelite®. Separating the solid curd from the liquid whey using rennet (a naturally occurring enzyme), formalin is then added which hardens the curds at a rate of around 1mm in thickness a week. This results in a button made from 96% milk! The whey, having many uses of its own, is then sold meaning nothing in the process goes to waste.
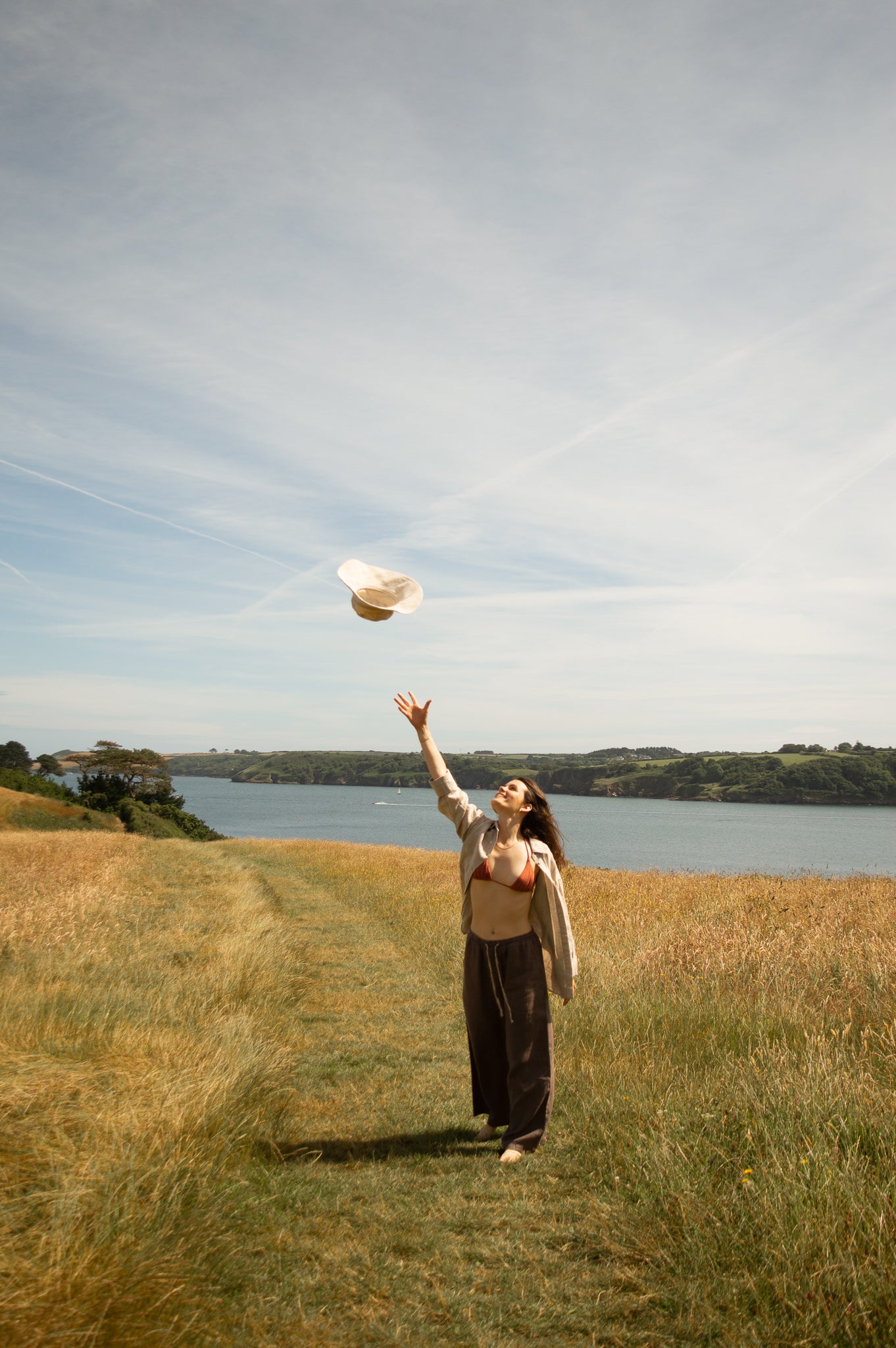
Robust and hard-wearing, Codelite® buttons behave much the same as their polyester rivals. Yet, unlike polyester, these little buttons are biodegradable, sustainable and traceable. Supporting British farmers, a sustainable English factory, as well as helping the environment…these are pretty superb buttons!
When visited by HRH The Princess Royal in 2019 David Courtney said: “Our ambition is to follow in the footsteps of our predecessors and make the finest buttons using the best quality materials available, while employing traditional techniques and processes.” I think it’s evident that David and Andrea have gone above and beyond in this and not only create the finest natural and ethical buttons (exceeding any plastic variety) but show the best of British in preserving our rich history and skills.
(additional photos courtesy of Courtney and Co)
Wear British buttons…
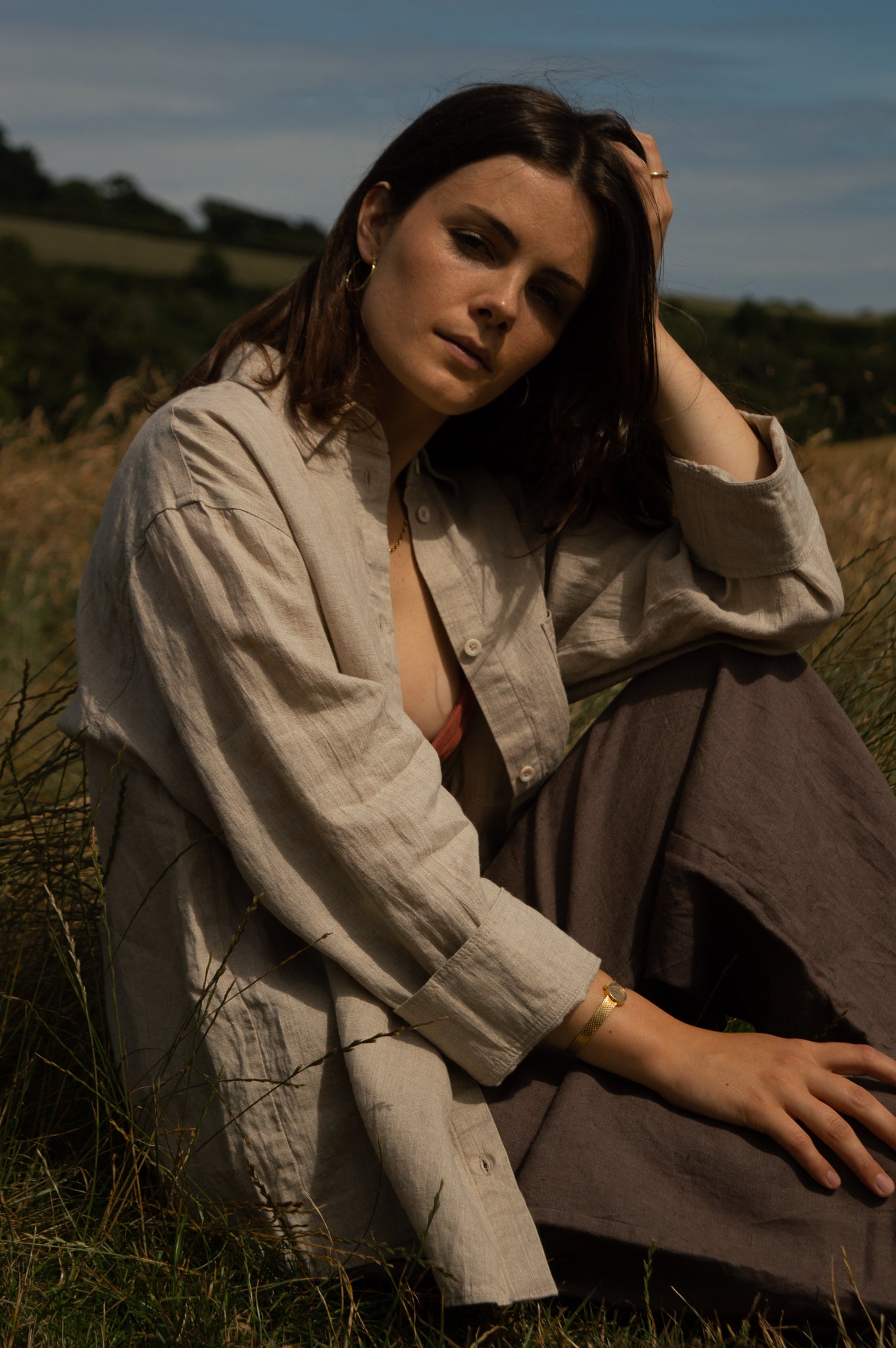
Saba Linen Shirt
Share

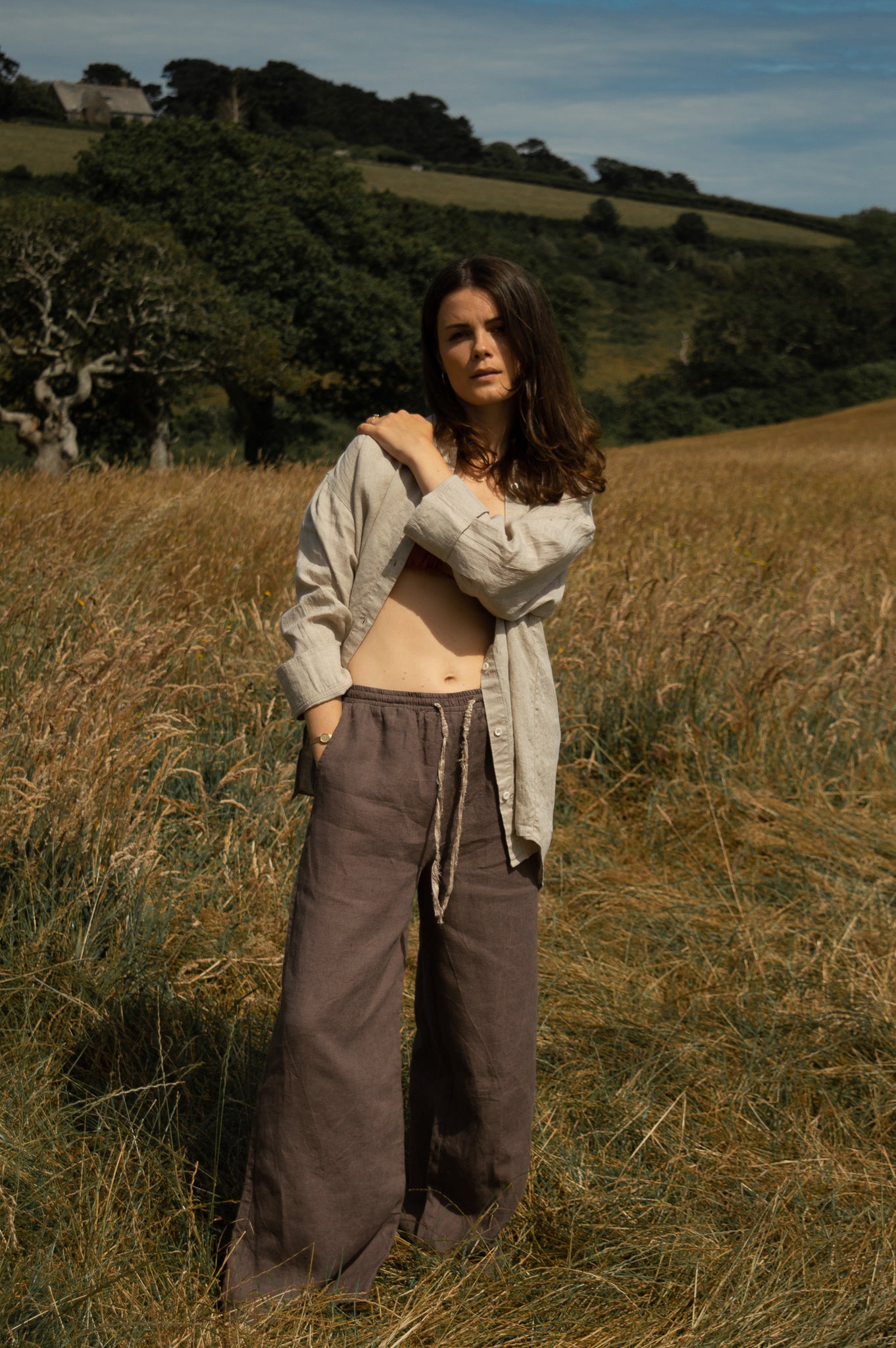

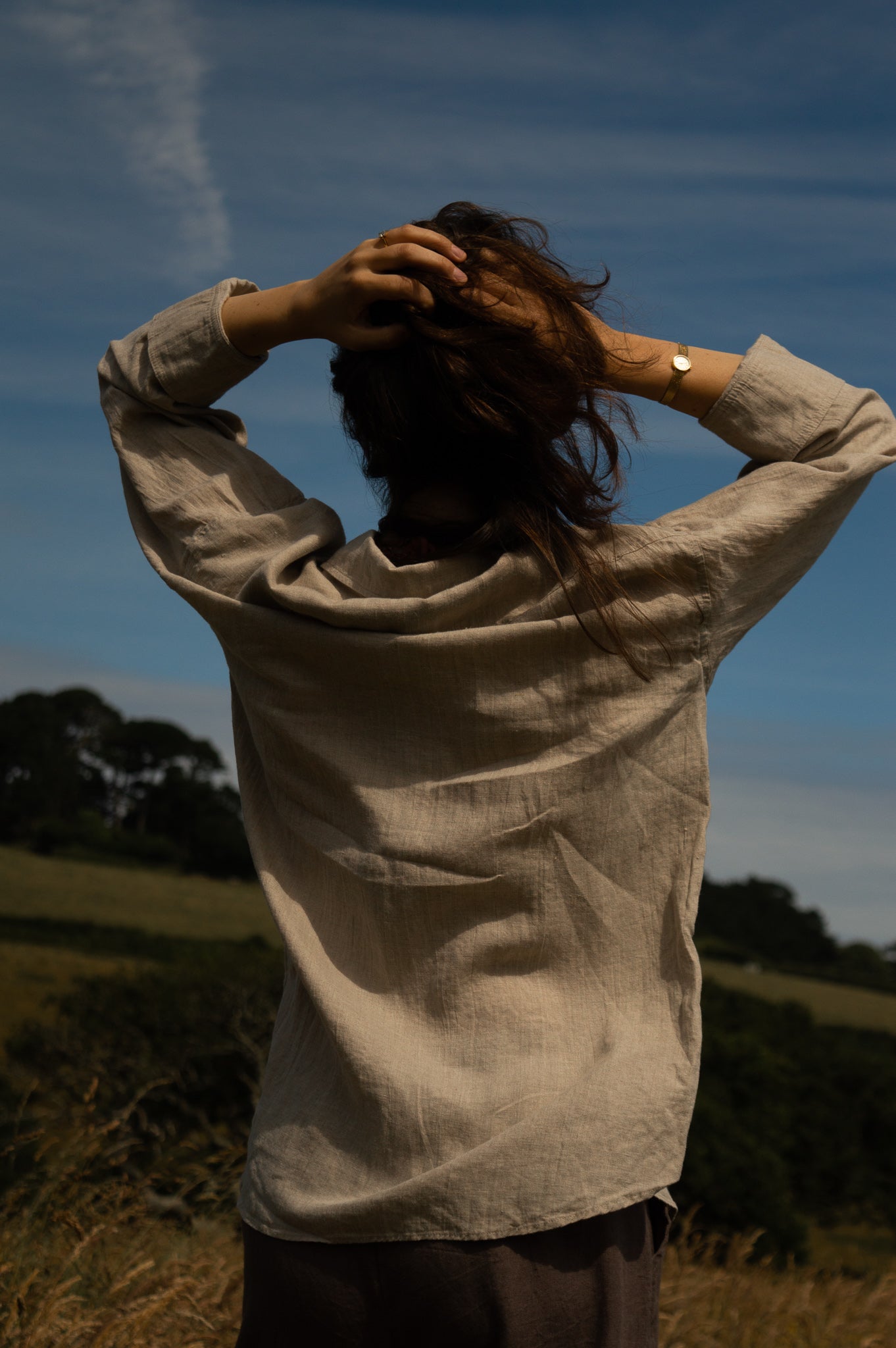
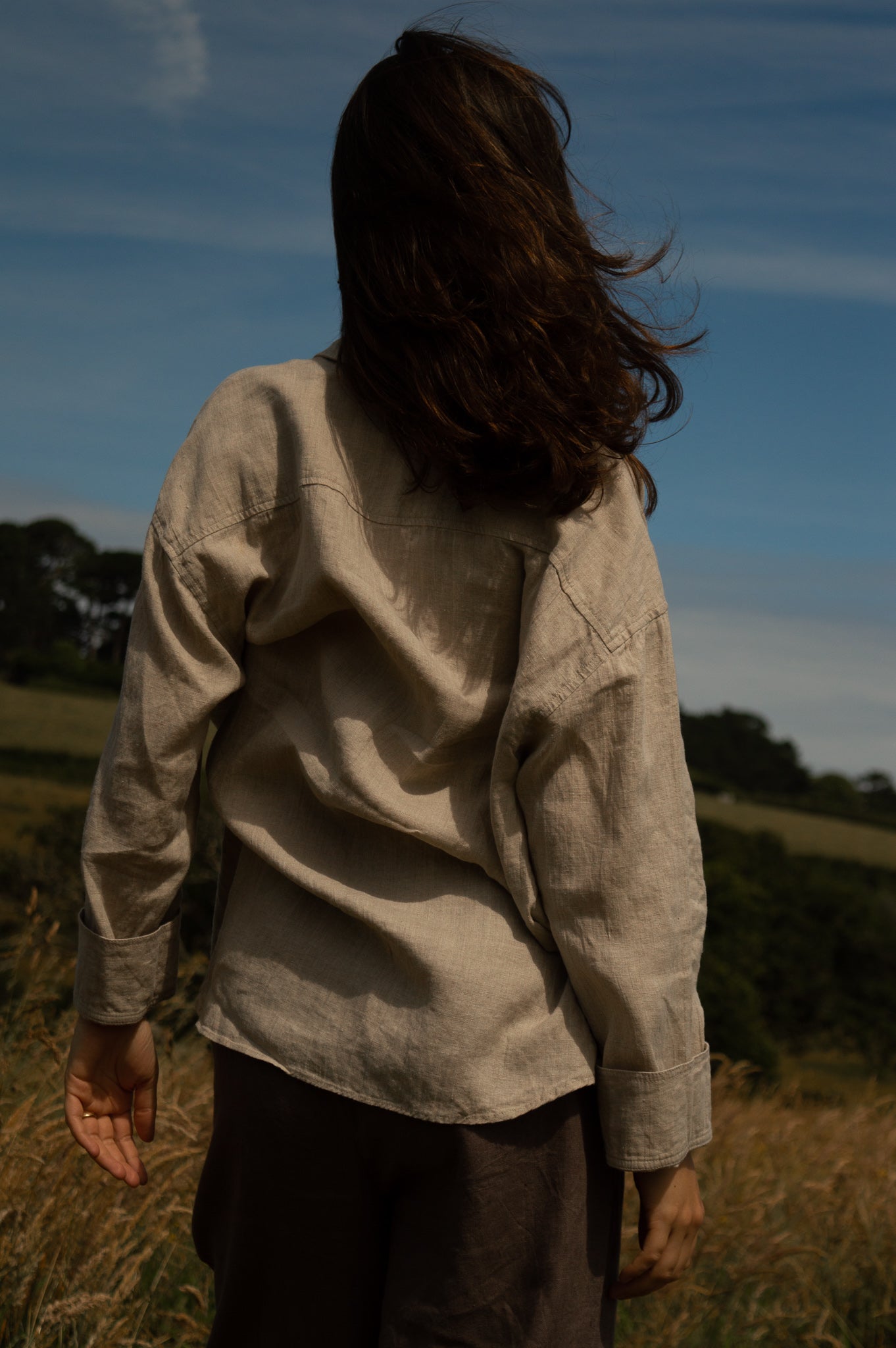
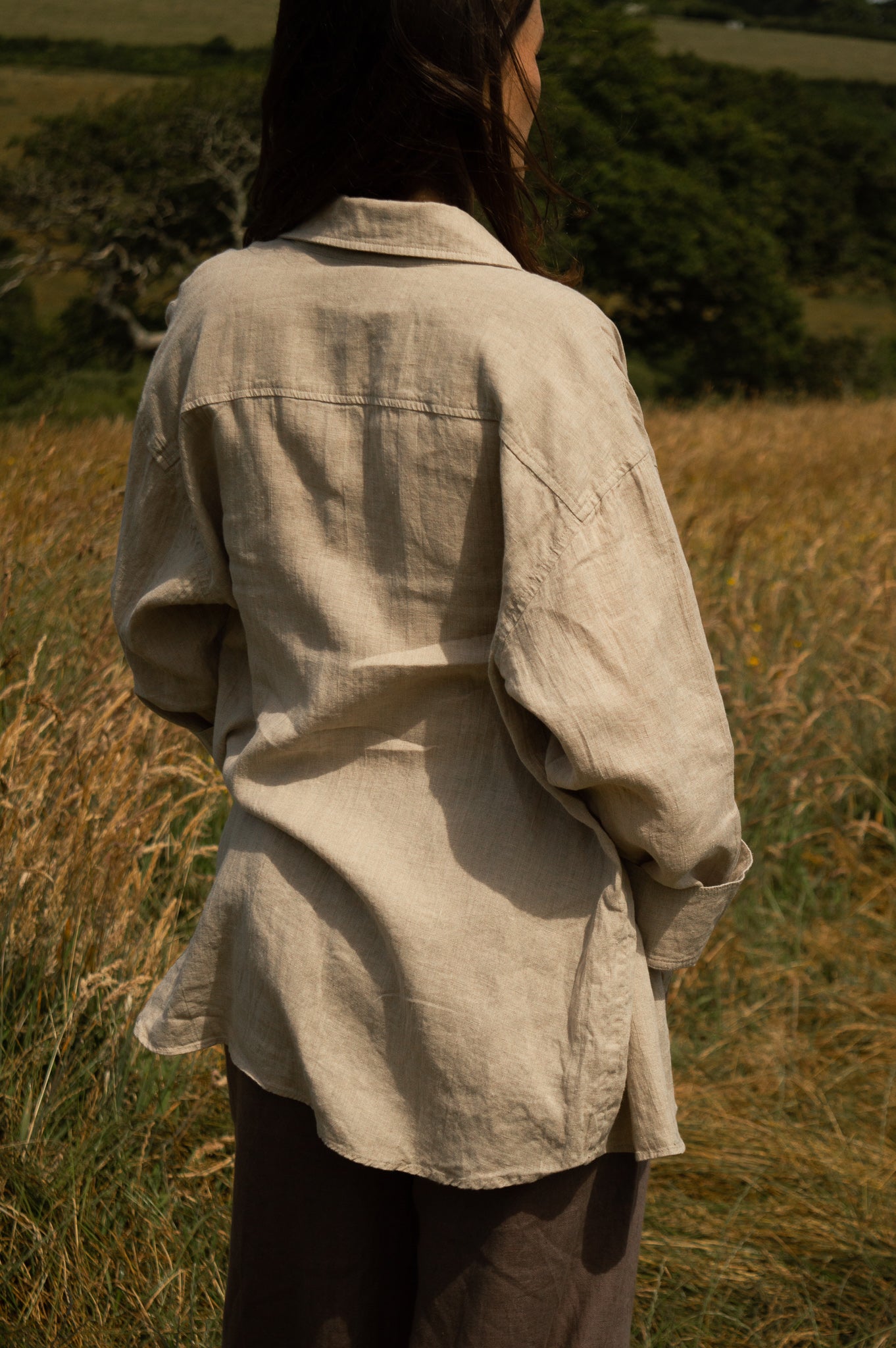
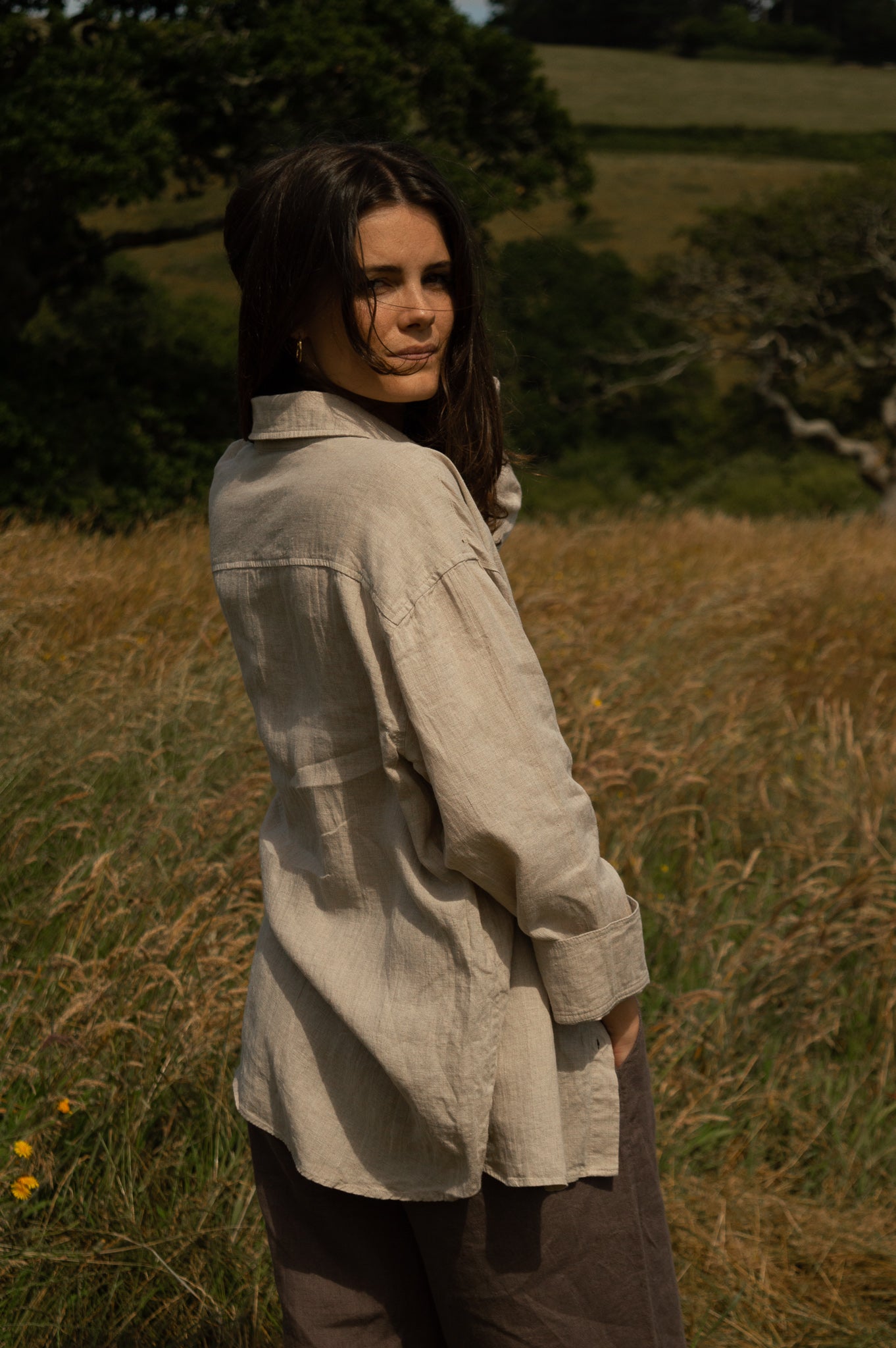
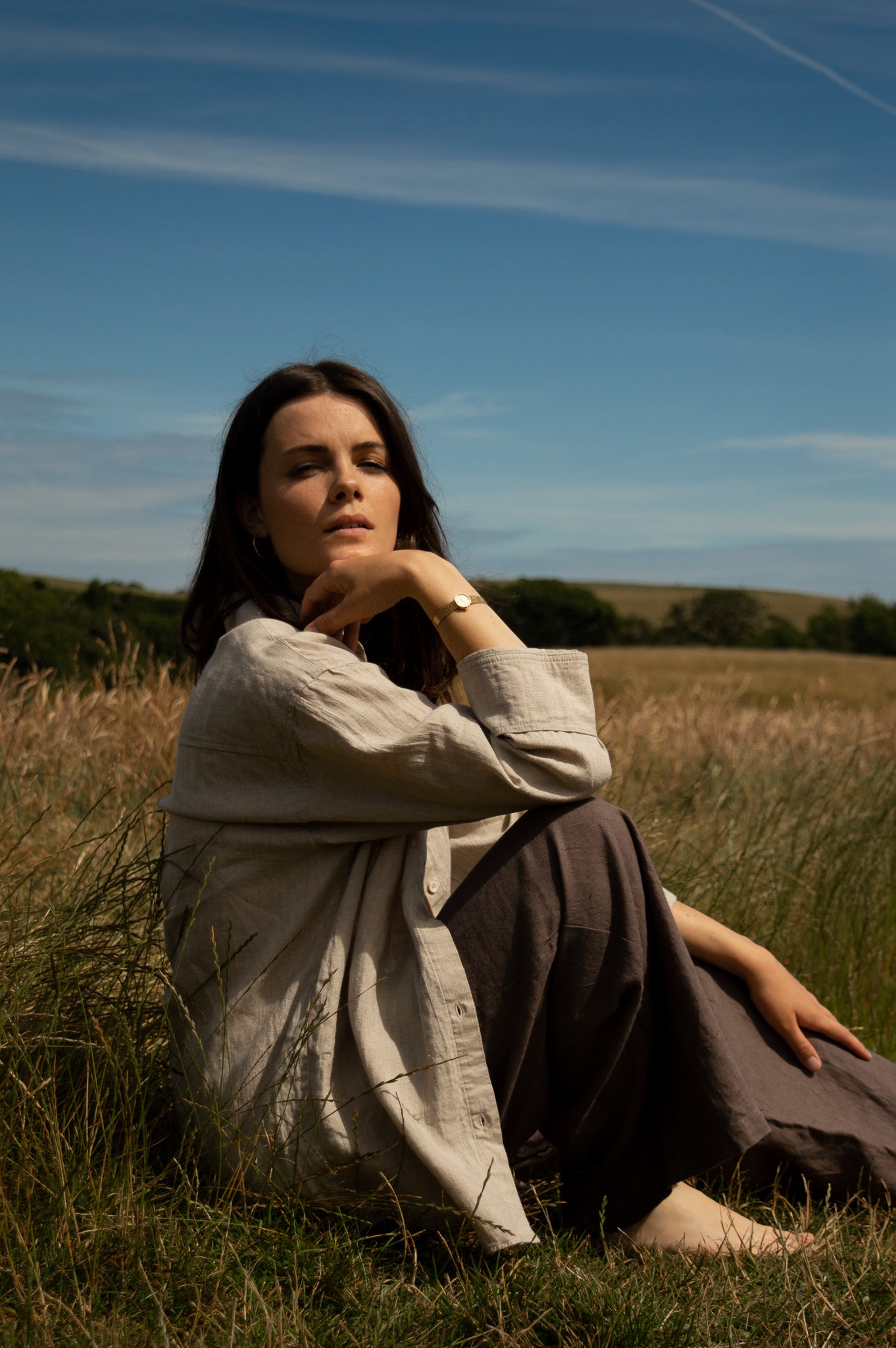
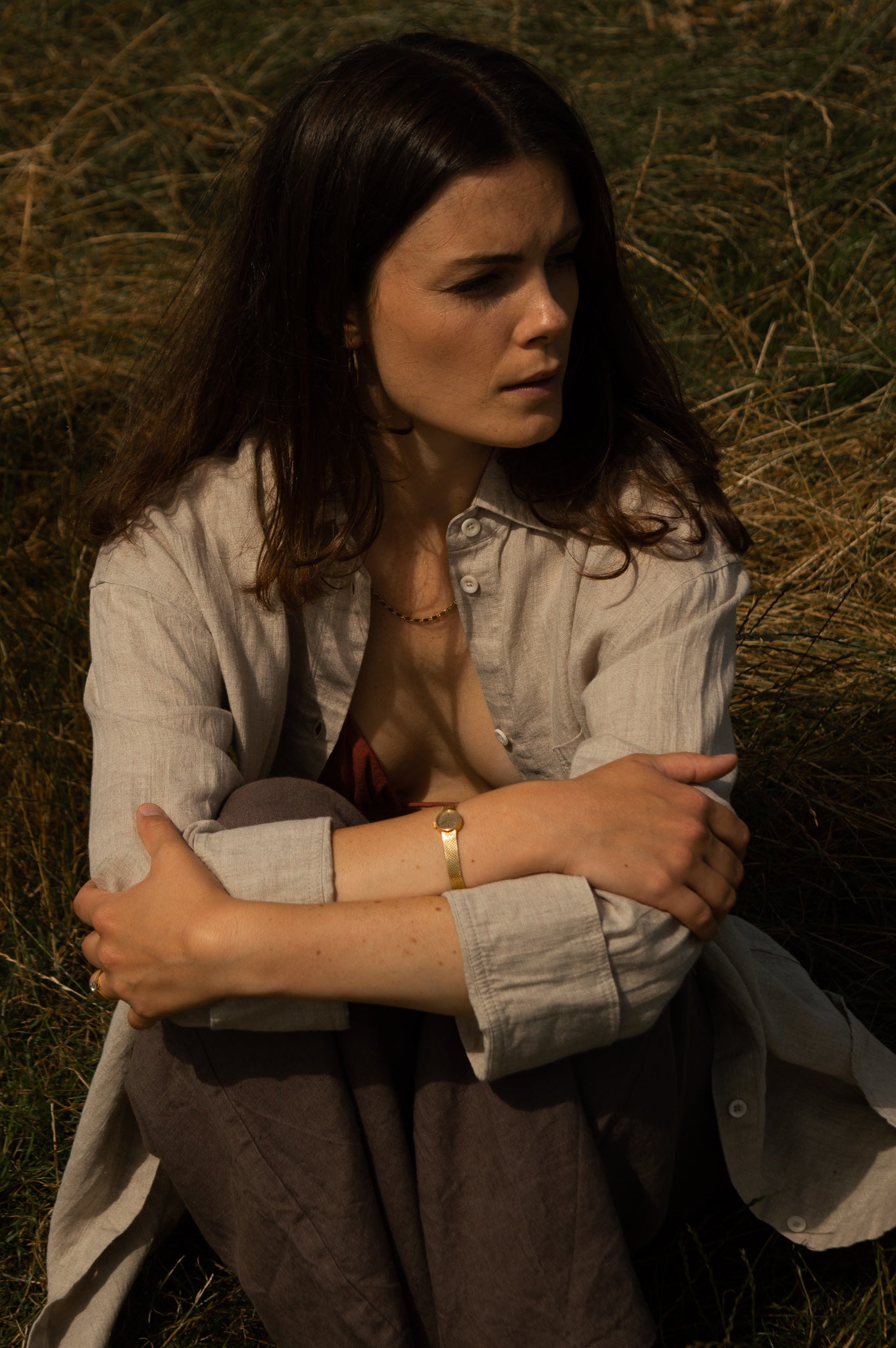
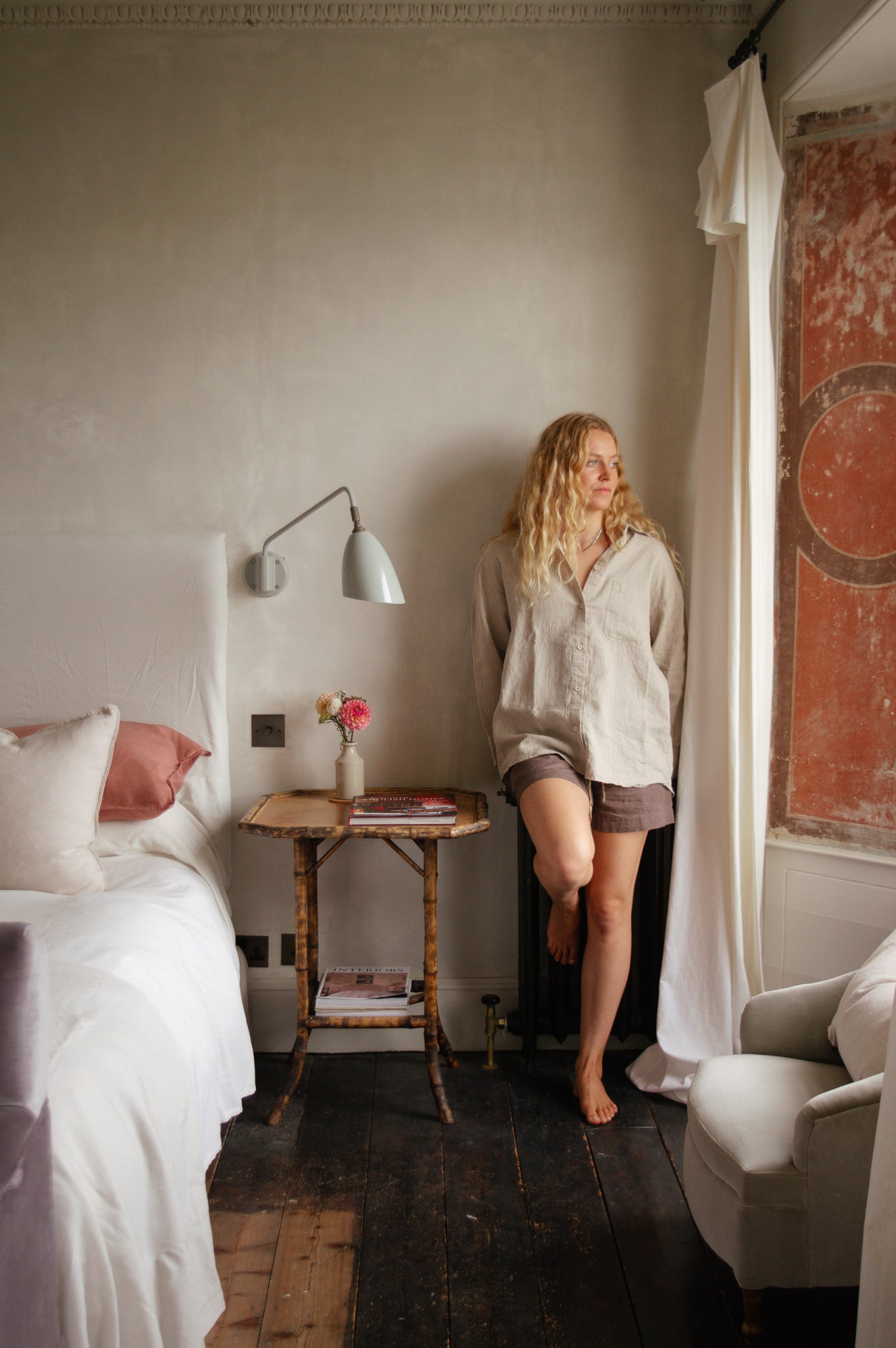
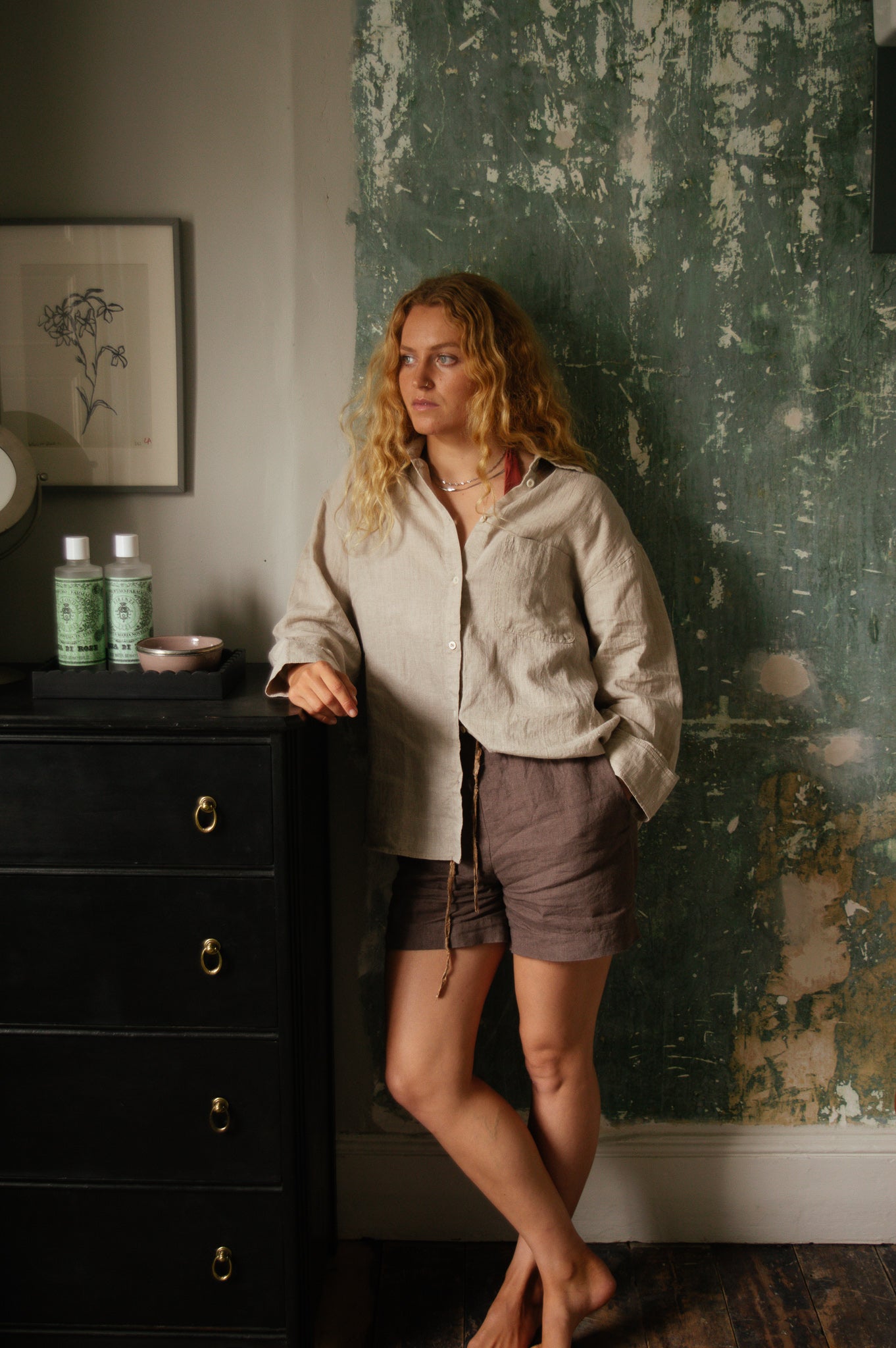
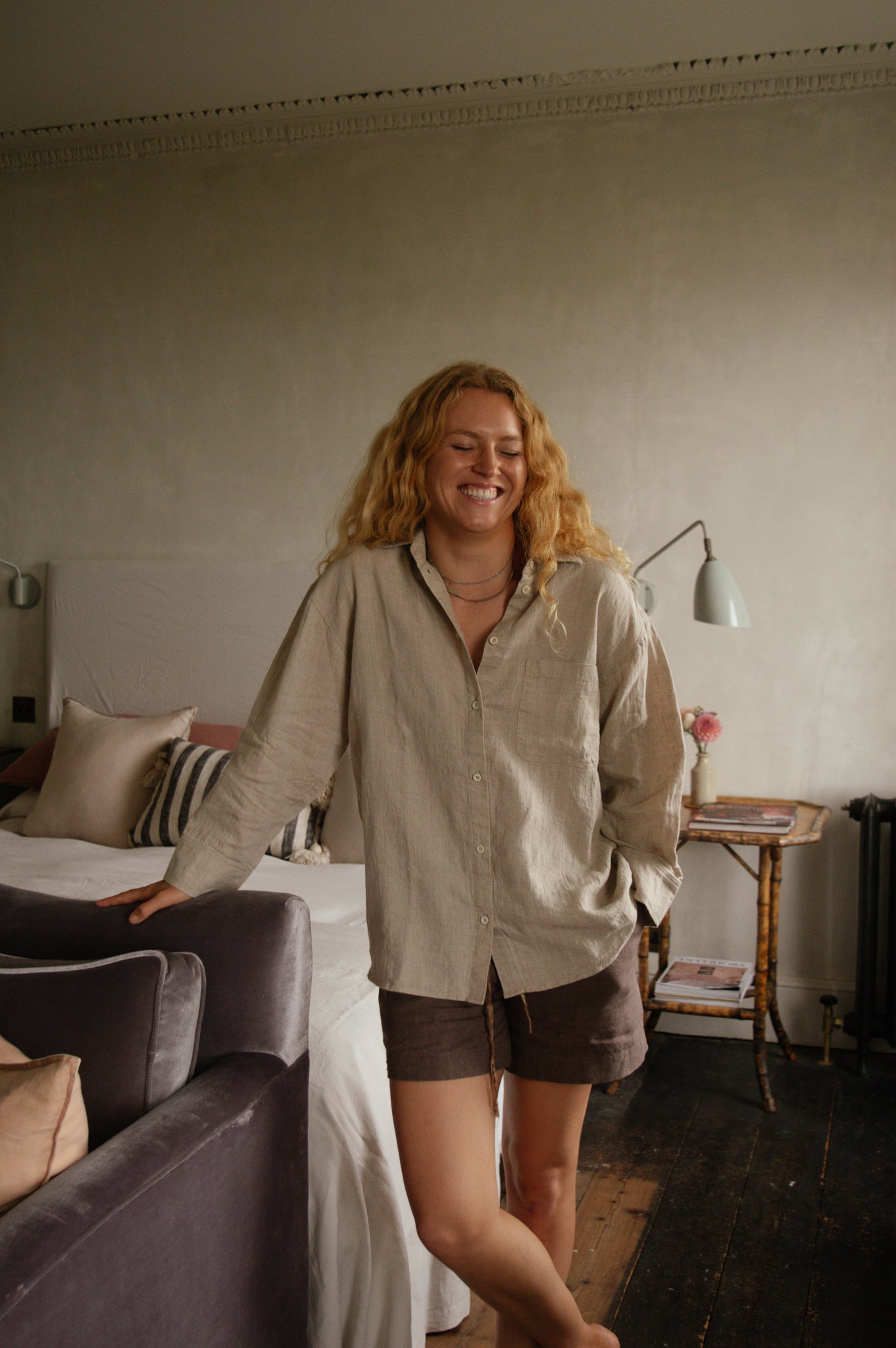
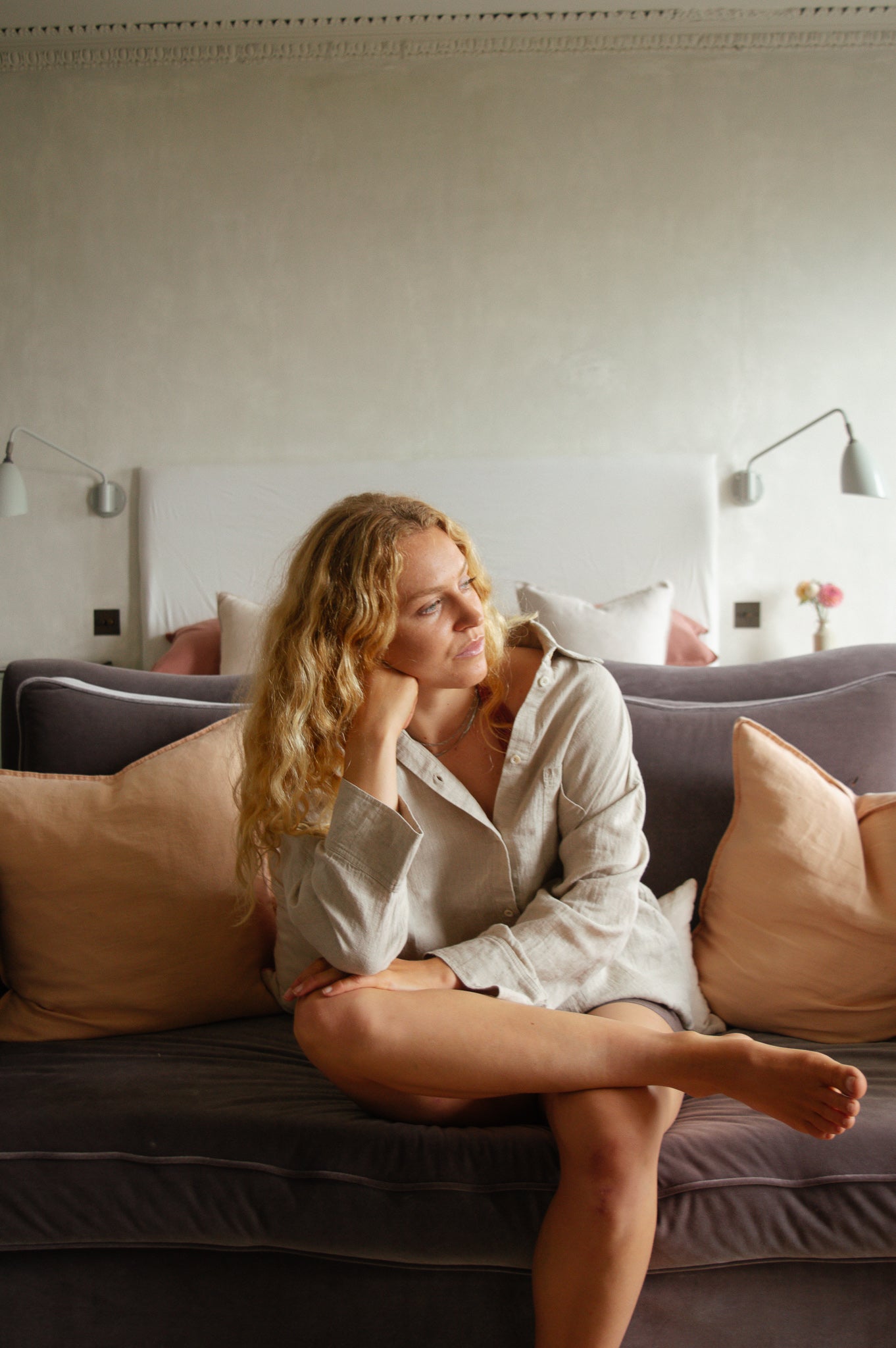
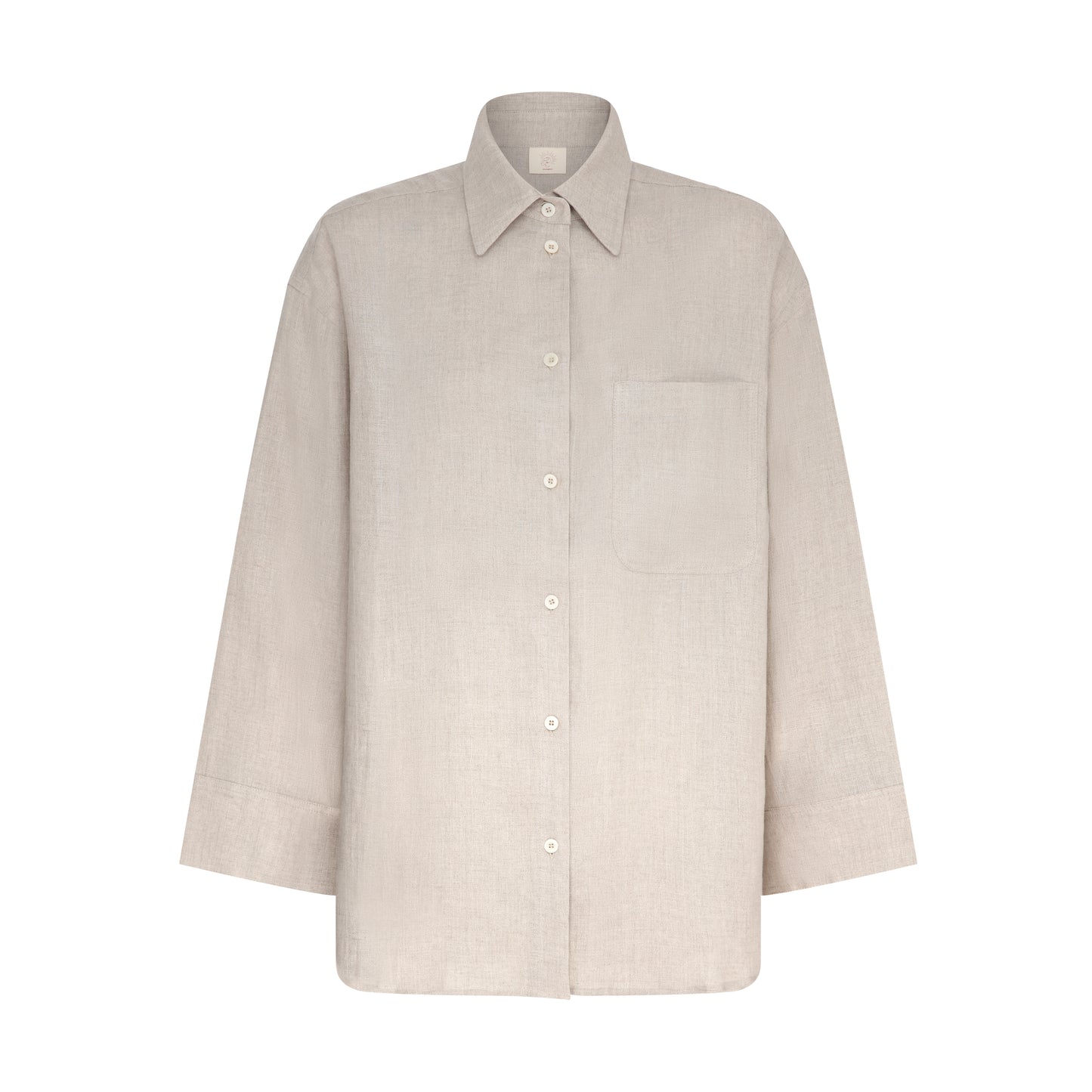