‘The bitterness of poor quality remains long after the sweetness of low price is forgotten’
Benjamin Franklin
Before starting Solpardus I had always thought I was pretty aware of the ethics surrounding clothing manufacturing and the various stages a garment would go through before it ended up in my wardrobe. But starting my own business was an amazing eye opener into just how many people work on one seemingly simple garment…

In the last decade, we have become far more aware of making good choices when buying food and clothes. Free-range, organic, fair-trade, cruelty-free; all things we know will be good choices. But how often do we really think beyond the labels we see on our purchases? When you think about it, it seems obvious that a high street retailer selling a bikini set for £5 is bound to have left someone (or many people) along the production line rather short. But when a designer bikini could set you back £500, and you still have no idea about its origins, it’s hard to work out where the fair price lies.
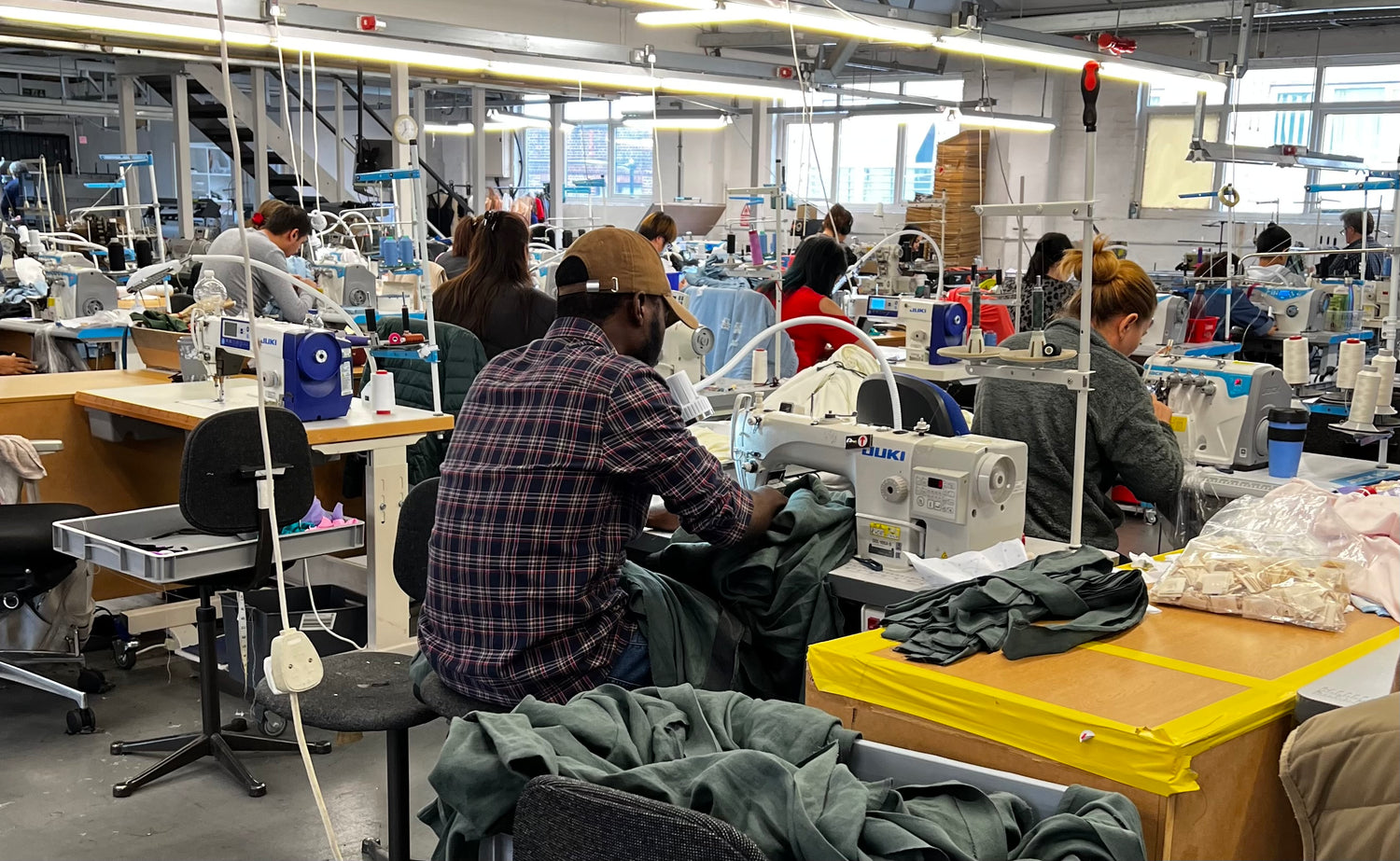
Investing in good quality will inevitably be more economical in the long run - less continuous purchasing, less waste, less disappointment. Unlike fast fashion, that works on the thrill of the purchase and keeping up with the latest trends, the slow fashion movement encourages ethical and conscious decision making when it comes to our shopping habits. Garments are made in small batches, to reduce waste, by well paid machinists in morally sound factories. These principles should stretch across the whole manufacturing process, from the original idea and fabric choices right through to the packaging and deliveries. At Solpardus we make sure everyone throughout the manufacturing process feels equally valued and appreciated, and that their quality work is rewarded.
The life cycle of a Solpardus garment….
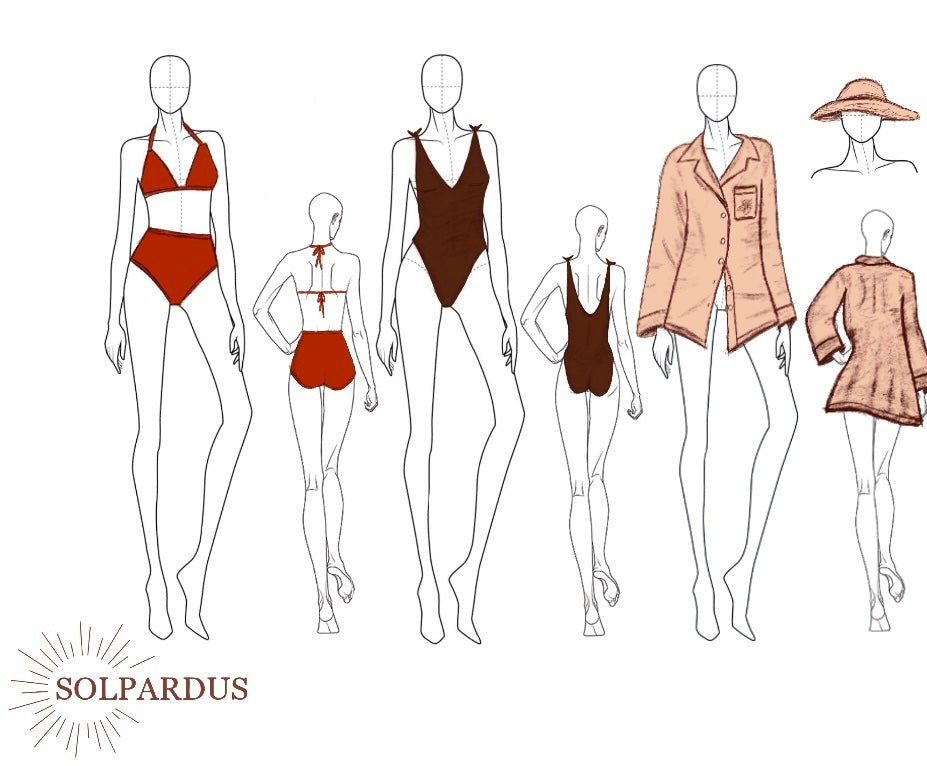
Freya mocks up a sketch of a garment at home in Cornwall
-
The sketch and notes are sent over to garment development to be turned into technical drawings
-
These technical drawings are then sent to the London manufacturer, along with fabric samples, for 3D development and pattern printing
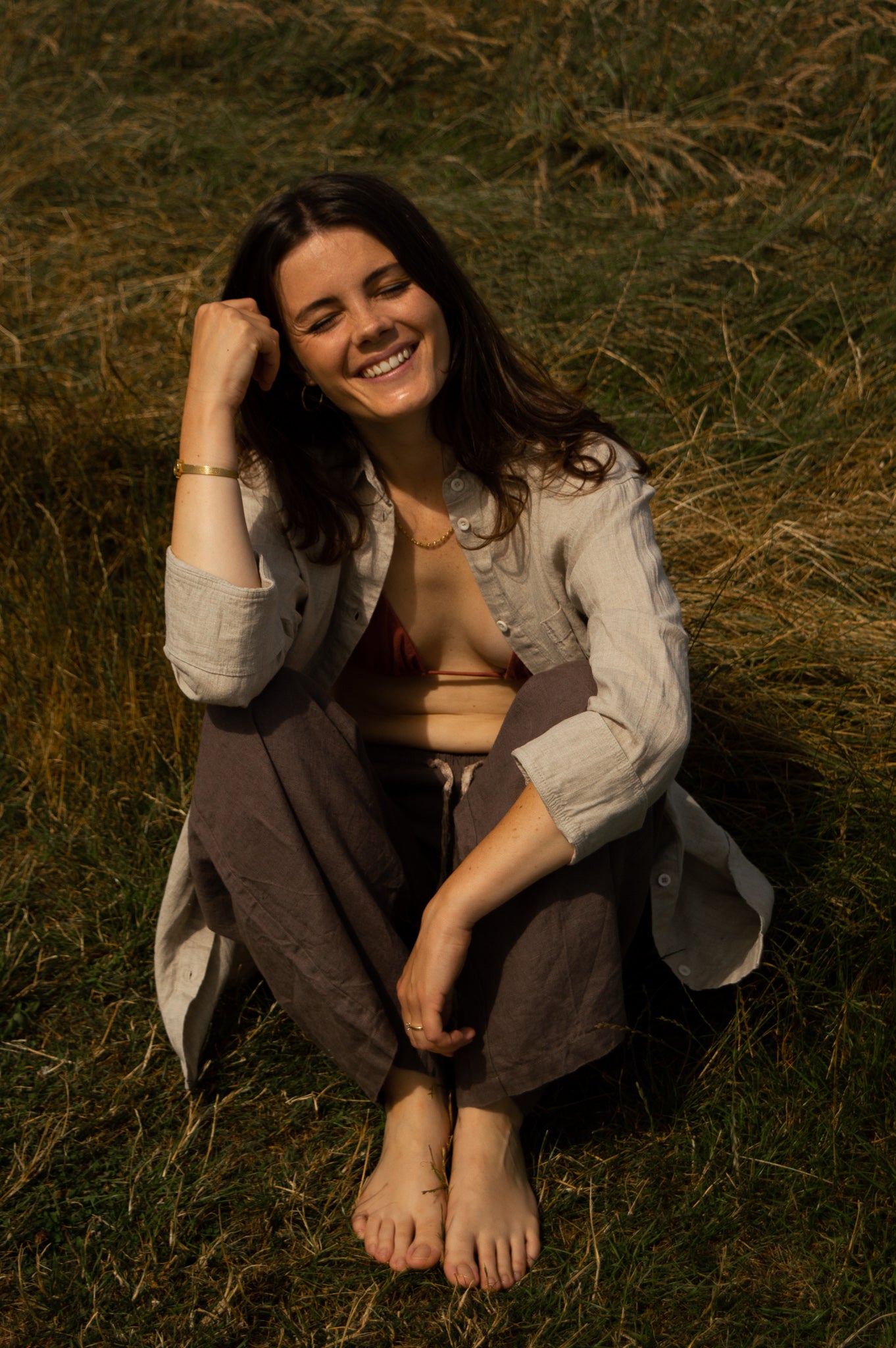
Once the 3D design has been approved, the London manufacturer then produces a sample garment (and perhaps another if any changes are needed)
-
Once the fit and style of the sample garment has been approved, Freya then sources bulk fabric and trim from British small businesses (within this, each material or item must also be produced by each independent manufacturer, including mocking up and then producing size and branding labels in Derby, and using British milk to make buttons in Gloucestershire)
-
Meanwhile, the sample garment pattern is sent to be graded so that different sizes can be produced
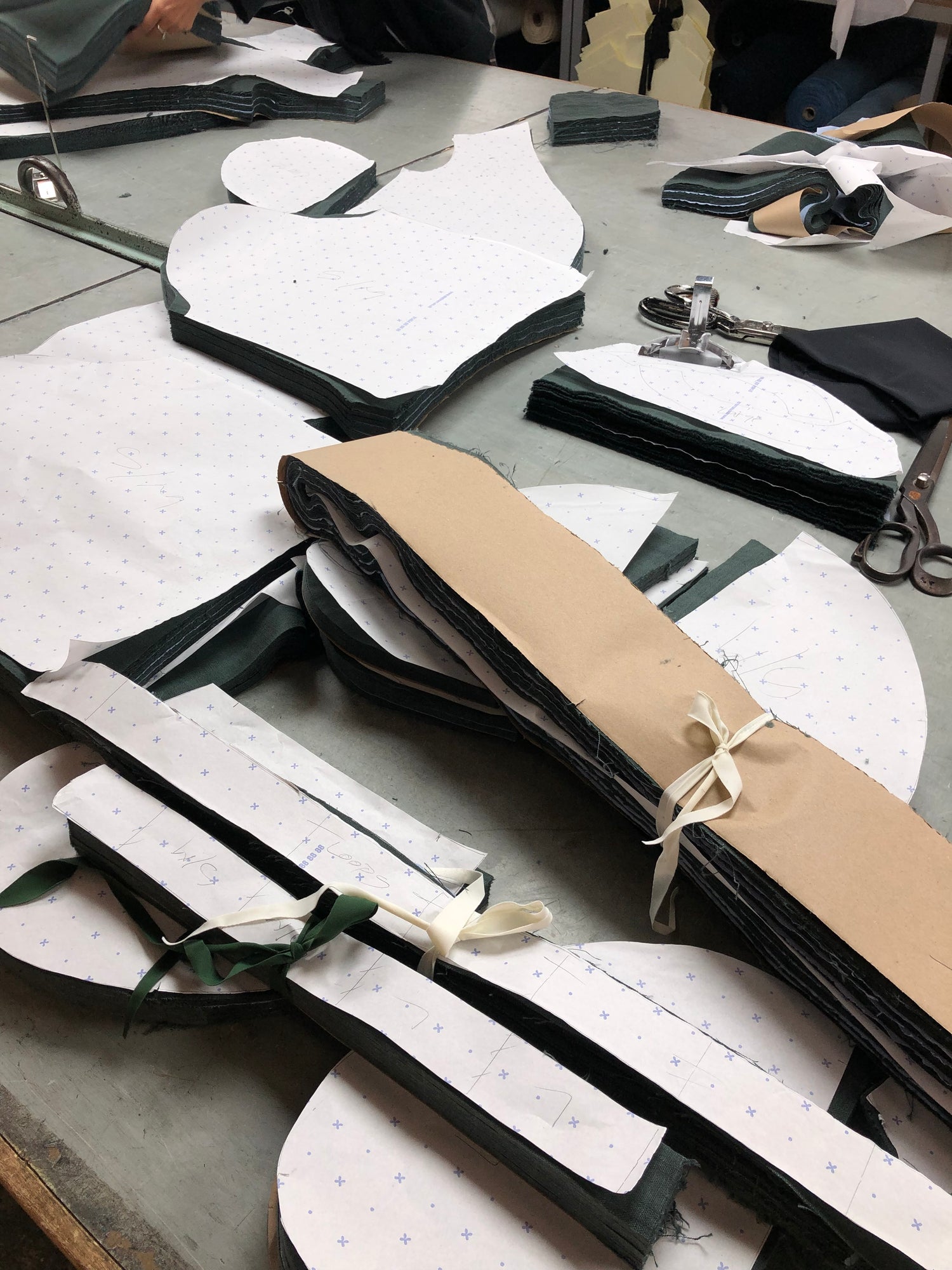
With the fabric, trim and pattern grading now all sourced, production in London can begin (this includes the pattern pieces being cut, sewn, any trim added, the garments being pressed and then boxed up to be transported down to Solpardus)
-
We then screenprint our cotton composition labels and boxes in house

Photography for the garment is organised (including a theme, location and sourcing models and props)
-
Finally, with photography back and everything ready to go, the garment is listed on our website and sent out to you from Cornwall, in ethically conscious packaging, to be worn and loved year after year!
Shop Ethical Fashion…
-
Bamboo Swimwear
Our super soft bamboo swimwear is perfect when you need to get...
-
Linen Clothing
Our linen collection is soft on your skin and provides the perfect...